What is Porosity in Welding: Recognizing Its Reasons and Enhancing Your Abilities
What is Porosity in Welding: Recognizing Its Reasons and Enhancing Your Abilities
Blog Article
Porosity in Welding: Identifying Common Issues and Implementing Ideal Practices for Prevention
Porosity in welding is a prevalent issue that often goes unnoticed till it causes considerable issues with the integrity of welds. In this discussion, we will certainly check out the essential aspects contributing to porosity formation, analyze its detrimental results on weld performance, and talk about the ideal practices that can be embraced to minimize porosity incident in welding procedures.
Common Reasons For Porosity

Making use of unclean or wet filler products can introduce pollutants into the weld, contributing to porosity concerns. To minimize these typical reasons of porosity, detailed cleansing of base metals, appropriate shielding gas option, and adherence to ideal welding criteria are important practices in attaining high-grade, porosity-free welds.
Impact of Porosity on Weld Top Quality

The presence of porosity in welding can dramatically endanger the architectural integrity and mechanical buildings of welded joints. Porosity produces voids within the weld steel, damaging its overall stamina and load-bearing capability.
One of the primary effects of porosity is a reduction in the weld's ductility and durability. Welds with high porosity levels often tend to display lower effect toughness and decreased capability to deform plastically prior to fracturing. This can be specifically concerning in applications where the bonded components are subjected to vibrant or cyclic loading problems. In addition, porosity can impede the weld's capability to effectively transfer pressures, leading to early weld failing and possible safety and security risks in critical frameworks.
Best Practices for Porosity Avoidance
To improve the architectural honesty and top quality of welded joints, what particular steps can be applied to minimize the occurrence of porosity throughout the welding process? Using the proper welding strategy for the specific product being bonded, such as changing the welding angle and weapon position, can better avoid porosity. Regular examination of welds and prompt removal of any kind of issues determined throughout the welding process are crucial techniques to avoid porosity and produce premium welds.
Significance of Proper Welding Techniques
Executing correct welding techniques is vital in ensuring the architectural honesty and top quality of bonded joints, building on the structure of effective porosity prevention measures. Welding techniques directly impact the overall strength and resilience of the welded structure. One key aspect of correct welding strategies is preserving the right warm input. Extreme warmth can bring about raised porosity due to the entrapment of gases in the weld swimming pool. On the other hand, inadequate warm may lead to incomplete browse this site fusion, developing prospective weak factors in the joint. Furthermore, using the suitable welding specifications, such as voltage, existing, and travel rate, is critical for attaining sound welds with very little porosity.
Moreover, the option of welding procedure, whether it be MIG, TIG, or stick welding, ought to straighten with the specific requirements of the task to make certain optimum results. Proper cleaning and prep work This Site of the base metal, in addition to picking the appropriate filler product, are likewise necessary parts of skilled welding methods. By sticking to these finest techniques, welders can reduce the risk of porosity formation and generate high-grade, structurally audio welds.
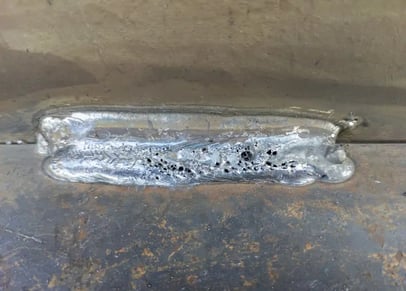
Evaluating and Quality Assurance Measures
Quality control actions play an essential function in confirming the stability and integrity of bonded joints. Testing treatments are necessary to find and avoid porosity in welding, making sure the stamina and longevity of the last item. Non-destructive testing approaches such as ultrasonic testing, radiographic testing, and aesthetic examination are frequently employed to identify possible flaws like porosity. These methods enable the evaluation of weld quality without compromising the honesty of the joint. What is Porosity.
Post-weld inspections, on the various other hand, examine the last weld for any defects, consisting of porosity, and verify that it meets defined standards. Applying a detailed top quality control plan that consists of complete testing treatments and assessments is vital to decreasing porosity problems and making certain the overall top quality of welded joints.
Conclusion
Finally, porosity in welding can be a common concern that influences the top quality of welds. By determining the usual sources of porosity and implementing finest practices for prevention, such as correct welding methods and screening actions, welders can guarantee excellent check my site quality and reliable welds. It is vital to prioritize avoidance approaches to minimize the incident of porosity and preserve the honesty of bonded structures.
Report this page